Scientists have designed a new material system to overcome one of the biggest challenges in recycling consumer products: mixed-plastic recycling. Their achievement will help enable a much broader range of fully recyclable plastic products and brings into reach an efficient circular economy for durable goods like automobiles.
We generate staggering quantities of plastic and plastic-containing products each year, but only a tiny fraction of that plastic can be recovered and used to manufacture products of similar quality. That’s because most products, from food-packaging films and single-use bags to sneakers and electronics, are made from mixtures of different plastics, and once they are mixed, those plastics can’t be recovered and used to make new bags or sneakers. Instead, most of it ends up in landfills, incinerators, or oceans.
A team of scientists from Lawrence Berkeley National Laboratory (Berkeley Lab) are tackling the mixed-plastic challenge using custom-designed material called polydiketoenamine (PDK), a new type of plastic they developed to be recycled efficiently and indefinitely, providing a low-carbon manufacturing solution for plastic products that never have to end up in a landfill.
In a new study appearing in Science Advances, the team showed that they can create customized PDKs specifically tailored for mixed-plastic recycling and that they can fully recover the constituent plastics from a blended product composed of multiple PDKs and other common manufacturing materials. Brett Helms, of the Molecular Foundry, headed up the multidisciplinary team, which also included researchers from the Joint BioEnergy Institute (JBEI) and Berkeley Lab’s Advanced Light Source, among others. The work is a major validation of a promising material and deepens our knowledge of polymer chemistry.
“We now know how to tailor PDK plastics in order to recycle complex products comprising several types of materials,” said Helms. “An example might be a shoe, where a textile is bonded to a rubber by an adhesive. Conventional materials used in such products can’t be recycled for reuse, since they can’t be deconstructed independently. Yet, if they were made from different, specially designed PDK polymers, then they could be for the first time.”
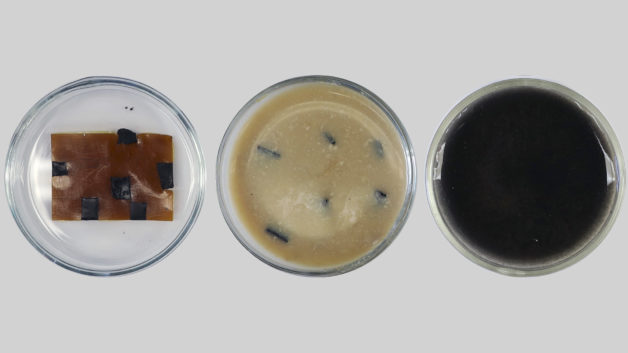
Creating a designer material
PDKs and other plastics are known as polymers, materials in which the constituent molecules are long chains of small repeat units known as monomers. For this work, the researchers started by making a variety of PDKs with slightly different chemical structures and showed that each could be “depolymerized” or broken down to its respective monomers with high yields of recovery. This is essentially the process of plastic recycling, as those recovered monomers can then be used to create a new batch of PDK.
The team found that each PDK depolymerized at a different temperature and rate. To better understand those properties, they used theoretical calculations and computational models (density functional theory) to simulate the different polymers and explore how they form and depolymerize. Using those theoretical insights, the team identified the best PDK molecules for the job and further optimized their design.
“A particularly nice aspect of this work was the tight integration between the experiments and computations,” said Molecular Foundry Director Kristin Persson, who led the theoretical work. “By uncovering the mechanism underpinning circularity, we were able to design new polymers that retain recyclability. We are excited that these design insights will inform future work.”
“It’s through those interactions between theory and experiment that we build the knowledge and the framework to establish the design rules governing polymer reactivity,” said Helms. “We would only have observations otherwise, rather than an explanation.”
Mixed plastics? No problem
Using those optimized molecules, the researchers demonstrated the success of their material system by creating blended plastics, each made from two different PDKs, and then completely depolymerizing and recovering the constituent materials. They repeated the demonstration with PDKs of different colors, addressing a particular industry challenge, and showed that with a slightly more complex process they could once again recover the PDK monomers with high yields.
The team also showed how PDK can be used to make recyclable, flexible plastic packaging out of conventional plastics. They formed a multilayer film from common plastics – polypropylene (PP) and polyethylene terephthalate (PET) – using a “tie layer” of PDK to bond them together. Normally the PP and PET couldn’t be extracted from a multilayer material, but here the researchers leveraged their control over the PDK layer to separate and recover the PP and PET films as well.
In a final demonstration of their powerful approach, the researchers constructed an object from a mix of different PDKs along with glass and stainless steel, to simulate the challenges of automobile recycling, and went through the recycling process again, demonstrating high-yield recovery of the PDK monomers as well as the glass and metal. These results could lead to a meaningful shift in how we approach the manufacture of durable goods, enabling a circular economy in which products are designed to be fully recovered and reused.
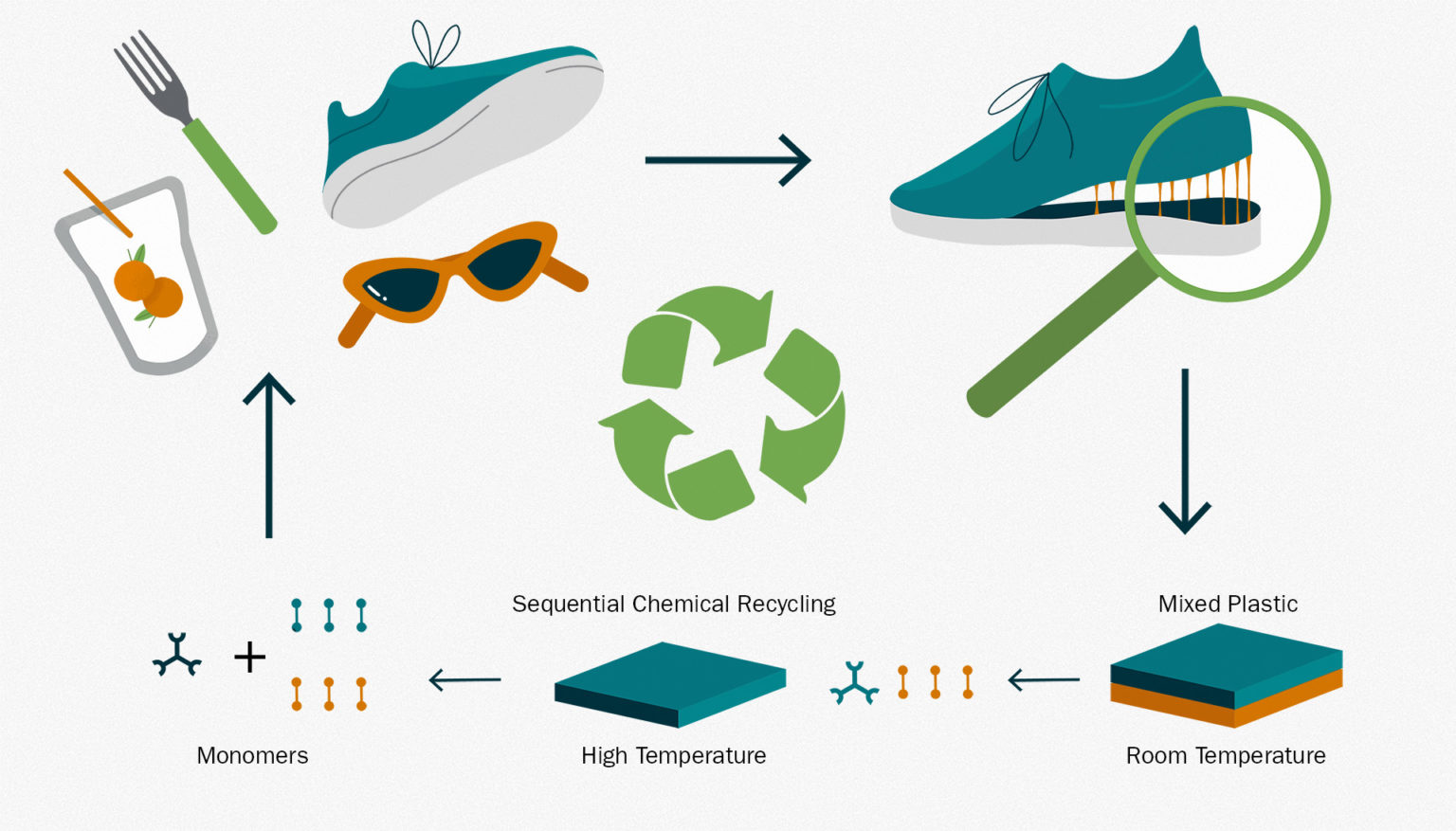
“Complex consumer products are simply not recycled today; they are either incinerated, landfilled, or downcycled,” Helms said. “Here we’ve laid the groundwork for how to recycle such products back to their original monomer building blocks, in stride facilitating the recovery of materials bound to them for reuse, including valuable metals or glass. In this way, PDK materials bring more circularity to manufacturing with intrinsically low carbon intensity.”
This research was supported in part by the U.S. Department of Energy’s (DOE) Office of Energy Efficiency & Renewable Energy and Berkeley Lab’s Laboratory Directed Research and Development program.
The Molecular Foundry and the Advanced Light Source are DOE Office of Science user facilities at Berkeley Lab. JBEI is a DOE Bioenergy Research Center managed by Berkeley Lab.
###
Founded in 1931 on the belief that the biggest scientific challenges are best addressed by teams, Lawrence Berkeley National Laboratory and its scientists have been recognized with 14 Nobel Prizes. Today, Berkeley Lab researchers develop sustainable energy and environmental solutions, create useful new materials, advance the frontiers of computing, and probe the mysteries of life, matter, and the universe. Scientists from around the world rely on the Lab’s facilities for their own discovery science. Berkeley Lab is a multiprogram national laboratory, managed by the University of California for the U.S. Department of Energy’s Office of Science.
DOE’s Office of Science is the single largest supporter of basic research in the physical sciences in the United States, and is working to address some of the most pressing challenges of our time. For more information, please visit energy.gov/science.
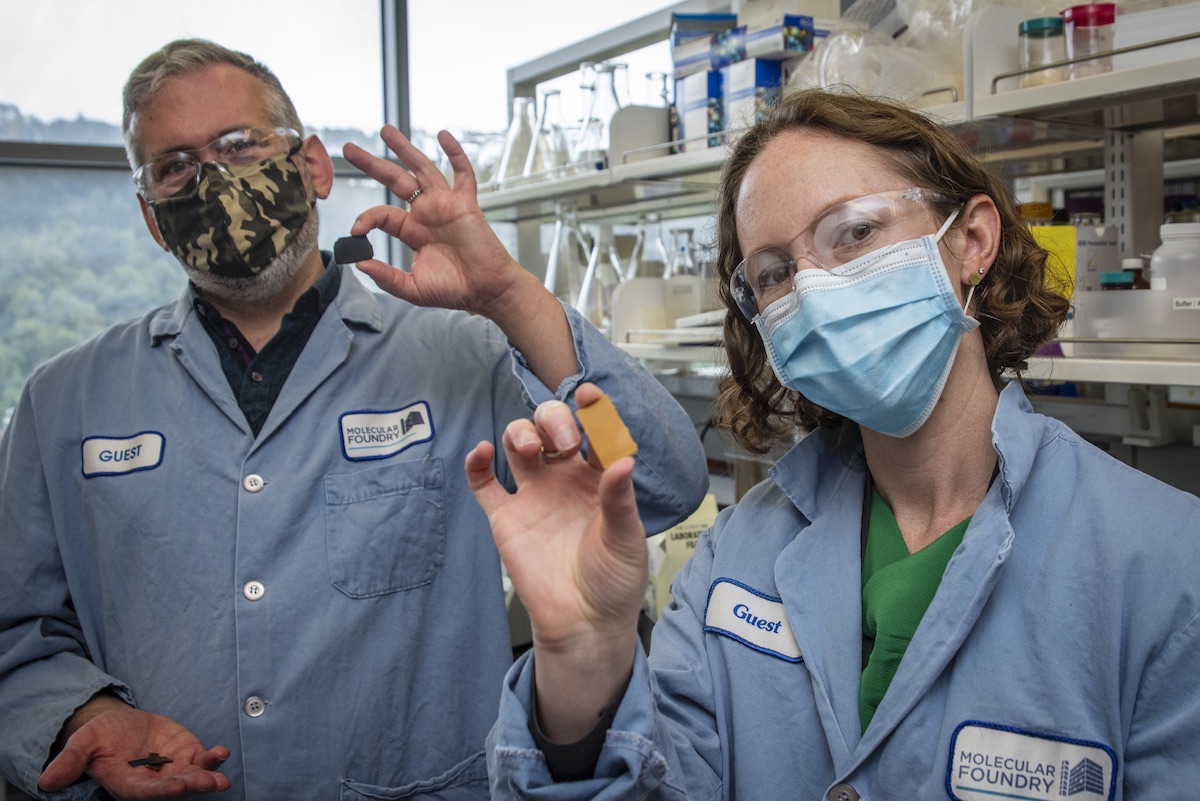
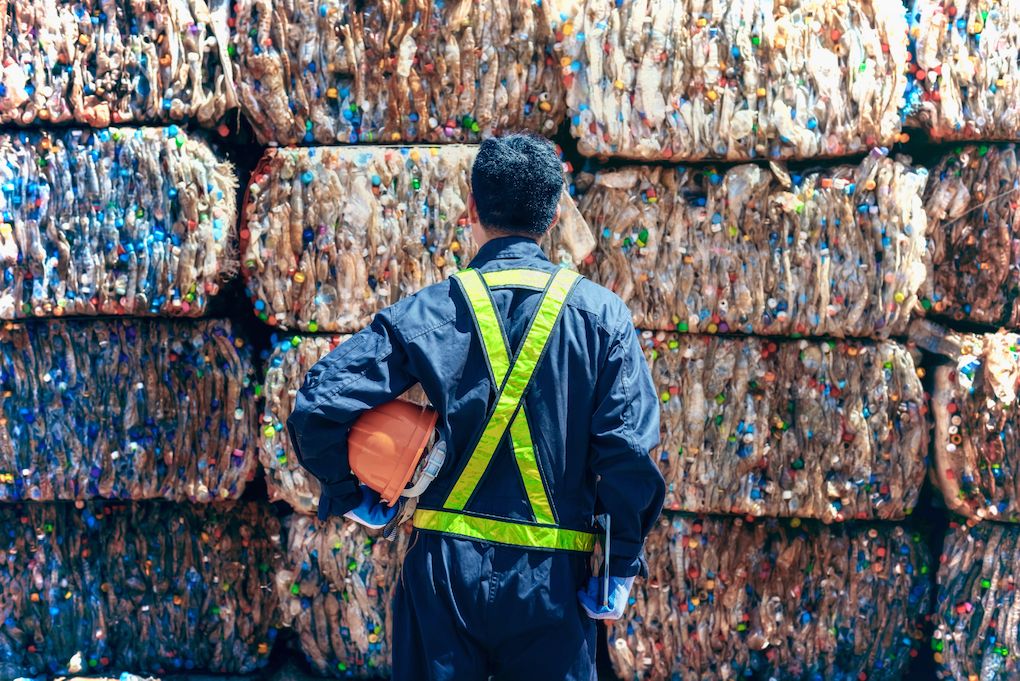
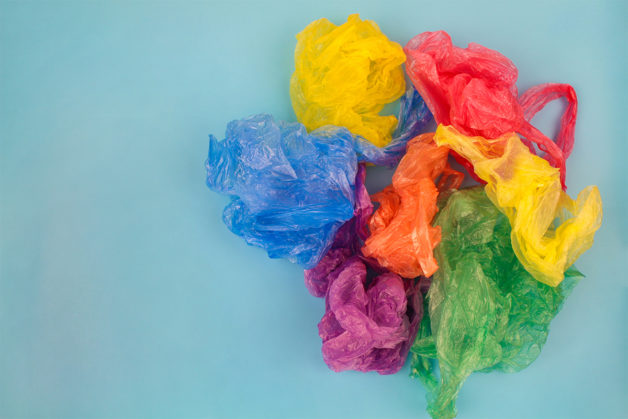